DIY sand casting process, which is the most traditional casting method, is a casting method in which sand is used as the main molding material to prepare a casting mold. Compared with sculpting wax for casting, due to its own characteristics (not limited by the shape, size, complexity and alloy type of parts, short production cycle and low cost), sand casting is still the most widely used casting method in casting production, especially for single or small bulk castings!
The basic process of the traditional sand casting process has the following steps: sand preparation, mold making, core making, modeling, pouring, sand falling, grinding processing, inspection and other steps. Let's take a look!
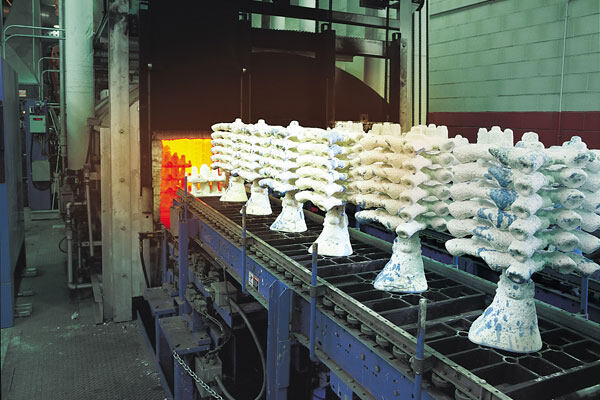
8 steps of sand casting process
- Sand mixing stage: prepare molding sand and core sand for modeling. Generally, a sand mixer is used to add the old picture and an appropriate amount of clay to mix.
- Molding stage: make molds and core boxes according to the parts drawings. Generally, wooden molds can be used for single pieces, plastic molds or metal molds (commonly known as iron molds or steel molds) can be made for mass production, and large-scale castings can be used to make mold plates. Now the molds are basically used engraving machines, so the production cycle is greatly shortened, and it generally takes 2 to 10 days.
- Modeling (core making) stage: including modeling (using sand to form the cavity of the casting), core making (forming the internal shape of the casting), and mold matching (putting the core into the cavity, and closing the upper and lower flasks together) ). Modeling is a key link in casting.
- Smelting stage: according to the required metal composition, the chemical composition is prepared, and the appropriate melting furnace is selected to melt the alloy material to form a qualified liquid metal liquid (including qualified components and qualified temperature). Smelting generally uses cupola or electric furnace (due to environmental protection requirements, cupola is now basically banned, and electric furnace is basically used).
- Pouring stage: use the molten iron ladle to pour the molten iron in the electric furnace into the formed mold. When pouring molten iron, you need to pay attention to the speed of pouring, so that the molten iron fills the entire cavity. In addition, pouring molten iron is more dangerous and needs to pay attention to safety!
- Cleaning stage: After the molten metal solidifies after pouring, take a hammer to remove the gate and shake off the sand of the casting, and then use a sandblasting machine for sandblasting, so that the surface of the casting will appear very clean!
- Casting processing: For some castings with special requirements or some castings that cannot meet the requirements, simple processing may be required. Generally, a grinding wheel or a polishing machine is used for processing and grinding to remove burrs and make the castings smoother.
- Casting inspection: The casting inspection is generally in the process of cleaning or processing, and the unqualified ones are generally found and picked out. However, some castings have individual requirements and need to be checked again. For example, some castings require the center hole to be able to insert a 5 cm shaft, then you need to take a 5 cm shaft and try to wear it.
In conclusion
After the above 8 steps, the casting is basically formed. For castings that require high precision, machining is required. With the advancement of casting technology, traditional diy sand casting is either improved or replaced by other casting methods, such as lost wax casting. Continuous innovation is the eternal theme, and it is the inherent quality and fundamental that our casting suppliers must have!